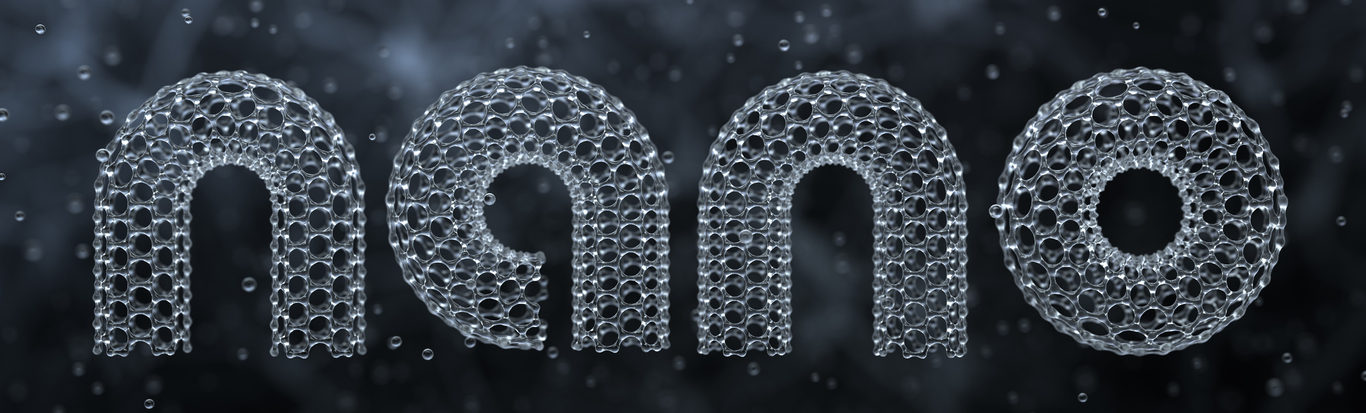
How ARMET Modifier Works
Armet modification process is based on the production of certain chemical compounds with the active elements of modifier which occurs in the melting process. These compounds have a significant deviation from the stoichiometric composition in the sense of lack of light elements, so crystallization at these centers requires much lower energy costs. This provides a high degree of coherence at the grain boundaries, the growth of inter-grain homogeneity, and the creation of modulated structure and, as a consequence, isotropy of cast parts.
A significant refinement of grains and sub-grains (coherent scattering regions) leads to an increase in the total area of grain boundaries and reduce the negative impact of unavoidable admixtures, reducing the amount of stress concentrators.
The melting process with Armet modifiers leads to a uniform crystallization throughout the volume of the casting, shifting the liquids and especially solids towards higher temperatures and narrowing intercritical intervals. This allows to obtain a high homogeneity of the material, substantially reduce the number of cracks, pores, cavities and increase the density and tightness of the casting.
The basis of Armet modifiers is a set of nanostructured powders of d- metal oxides in various composition and the ratio, as well as reductants. As you enter the modifier in the melting process, the dissociation of reducing agents starts resulting in restoring the active elements from the oxides in the melting temperature, which forms carbides in iron and steel, or intermetallic compounds in aluminum alloys, producing multiple centers of crystallization and decreasing melting temperature.
The use of d-metal oxides in the form of nanostructured powders significantly improves the efficiency of the modifiers and reduce their consumption rate, allowing for doping at the micro level (microalloying).
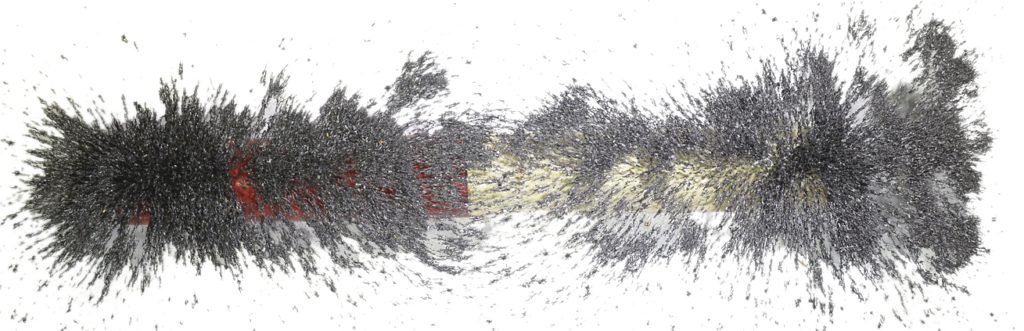
ARMET modifier for Iron, Steel & Aluminum alloys
The main objective of Armet modifier is to improve the quality of casting by decreasing foundry defects, improving operating properties of cast parts and extending the service life of the parts.
In particular,
- Adding 0.2% of Armet modifier in the molten iron process leads to a significant reduction of foundry defects.
- Adding 0.3% – 0.5% of Armet modifier improves the mechanical and operational characteristics of casting e.g:
– increases strength by 4 – 6 units
– increases abrasive wear resistance by 2-3 times - Adding 0.1% – 0.3% of Armet modifier in the molten steel enhances the impact toughness of the casting material up to 80% (within a climate temperature under 40°F) and up to 50% (within a climate temperature under 75°F).
For example:
- The service life of mixer blades reinforced with plates of the Armet modified iron is 70-75 working shifts of continuous operation as compared with 15-20 shifts of operation in case of serial blades in a 7 hour workday at silicate brick factories.
- The hydro-cyclone cone nozzles produced with Armet modifier worked for
24 months (in a continuous working cycle) in Arctic regions, instead of 1.5 months in case of conventional nozzles.
- The service life of flow duct parts for slurry pumps (impeller, casing, armor) produced with Armet modifier is 900 hours as compared with 420 hours for parts of high-chrome nickel-alloyed cast iron.
Microstructure Analysis
Picture 1
Mn18Cr2 without Modifier
zoomed in X200
Picture 2
Mn18Cr2 without Modifier
zoomed in X500
Picture 3
Mn18Cr2 with ARMET Modifier
zoomed in X200
Picture 4
Mn18Cr2 with ARMET Modifier
zoomed in X500
Pictures 1 and 2 shows the structure of the sample demonstrating grains of dendritic (highly branched structure).
Pictures 3 and 4 shows the structure of the sample which has the grains with an equiaxial shape without branching.
Conclusion: the usage of Armet modifier in the melting process creates the steel with a structure more favorable for mechanical properties: there is no pronounced heterogeneity of the dendritic structure, rounded inclusions of graphite which reduces the internal stress concentration when an external load is applied.