ARMET Foundry produces tailings processing equipment parts for Alaska gold mine
ARMET’s foundry Chicago office has secured a contract to deliver three “Vertical Plate Pressure Filters’ with all the associated equipment for dry tailings processing to POGO Gold Mine in Alaska.
POGO is a greenfield project owned and operated by Northern Star. It is a blind epithermal gold and silver deposit in the Tintina Gold Province of Alaska.
The contract has been booked under the Chicago Office second quarter orders. The pressure filters are set for commissioning in October 2022.
POGO technical manager Frank James said: “POGOS’ vision is to be the global leader in sustainable gold mining. The POGO project is located in the Tintina Mountains, where water is scarce.
“To minimize the use of water and improve the physical and chemical stability of our tailings, we have decided to adopt filtered tailings for the project. POGO will be a benchmark plant for dry tailings processing.”
According to ARMET Foundry, POGO is an exciting project for the company to work on as it considers dry tailings as one of the ‘most socially responsible and economically viable’ solutions for the management of tailings.
ARMET’s Mining Equipment senior manager Oswald von Starck said: “The location of the plant at a height of almost 5km above the sea level comes with its own unique challenges. For example, the design and transportation of the equipment as well as commissioning needs to be done with special care.
How Armet’s wear parts helping Aggregate & Mining Industries to reduce operational costs?
Armet wear parts helping the Aggregate & Mining Industries
ARMET wear parts is helping the Aggregate & Mining Industries to save more in operational expenses with our long lasting wear parts made with Armet Modifier which intensifies the strength, resistance and life cycle of the parts.
ARMET’s foundry manufacturing wear-resistant parts occupies a lot space of 33 thousand square meters, where the production area is 12,000 square meters and office space is 4,000 square meters. The annual production capacity exceeds 30,000 tons. The plant utilizes advanced equipment to control the chemical composition and physical mechanical properties of the products, ensuring their quality and reliability.
ARMET has a facility specifically dedicated to the research, development and manufacture of advanced modifiers, which are used in ARMET advanced technologies for achieving excellent operational results and optimal product quality.
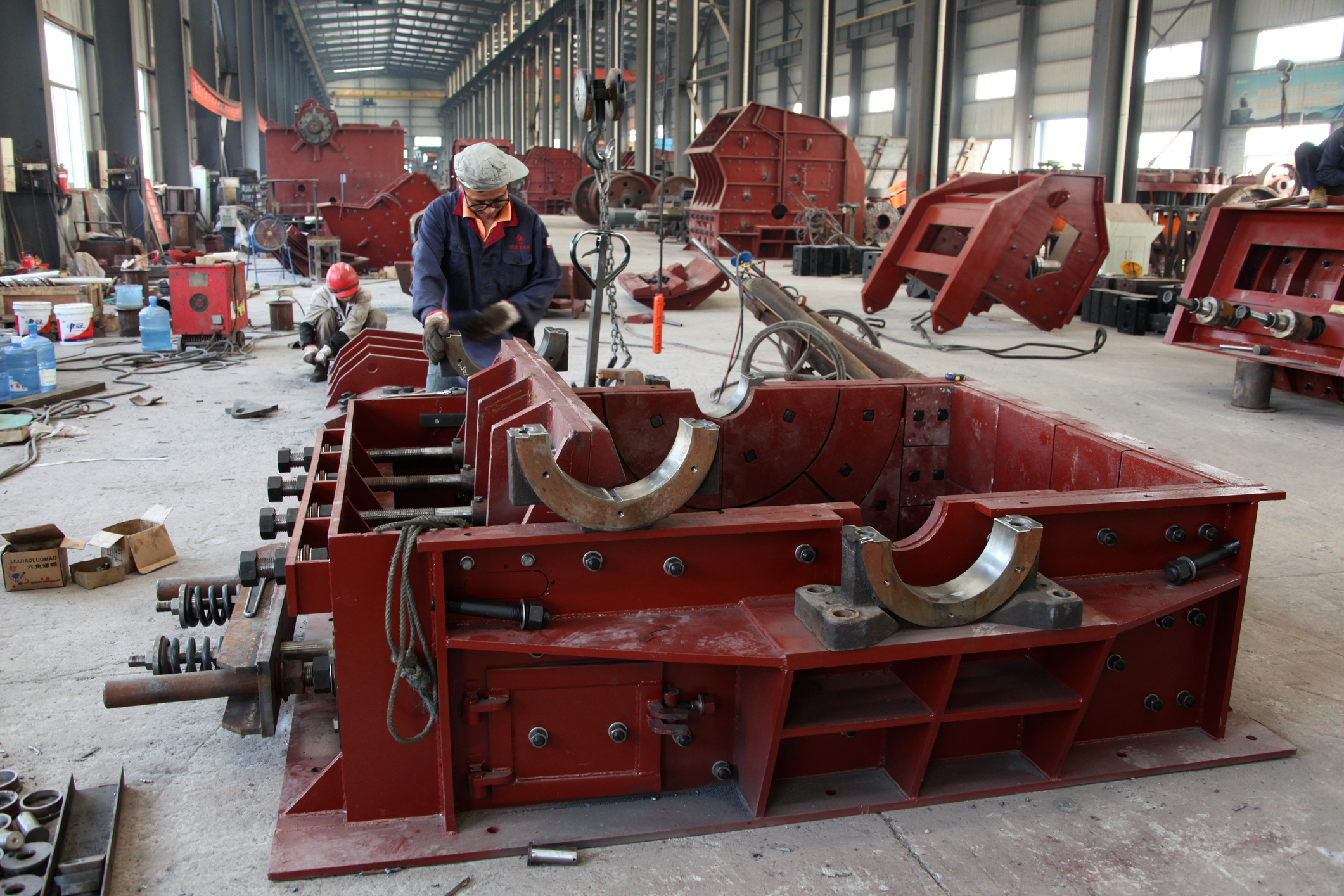
The target markets of ARMET high-quality wear-resistant casting products include countries in Asia, North and South America, Europe and the CIS. ARMET main products are produced with high-manganese steels, high-chromium cast irons, other alloy steels, composite materials and additional alloys generating wear-resistant products applied in mining, electric power provision, construction and other industries.
ARMET employs highly qualified management and engineering staff, hailing from a variety of countries, whose expertise fosters continuous product improvement, with focus on optimizing wear-resistance and overall quality.
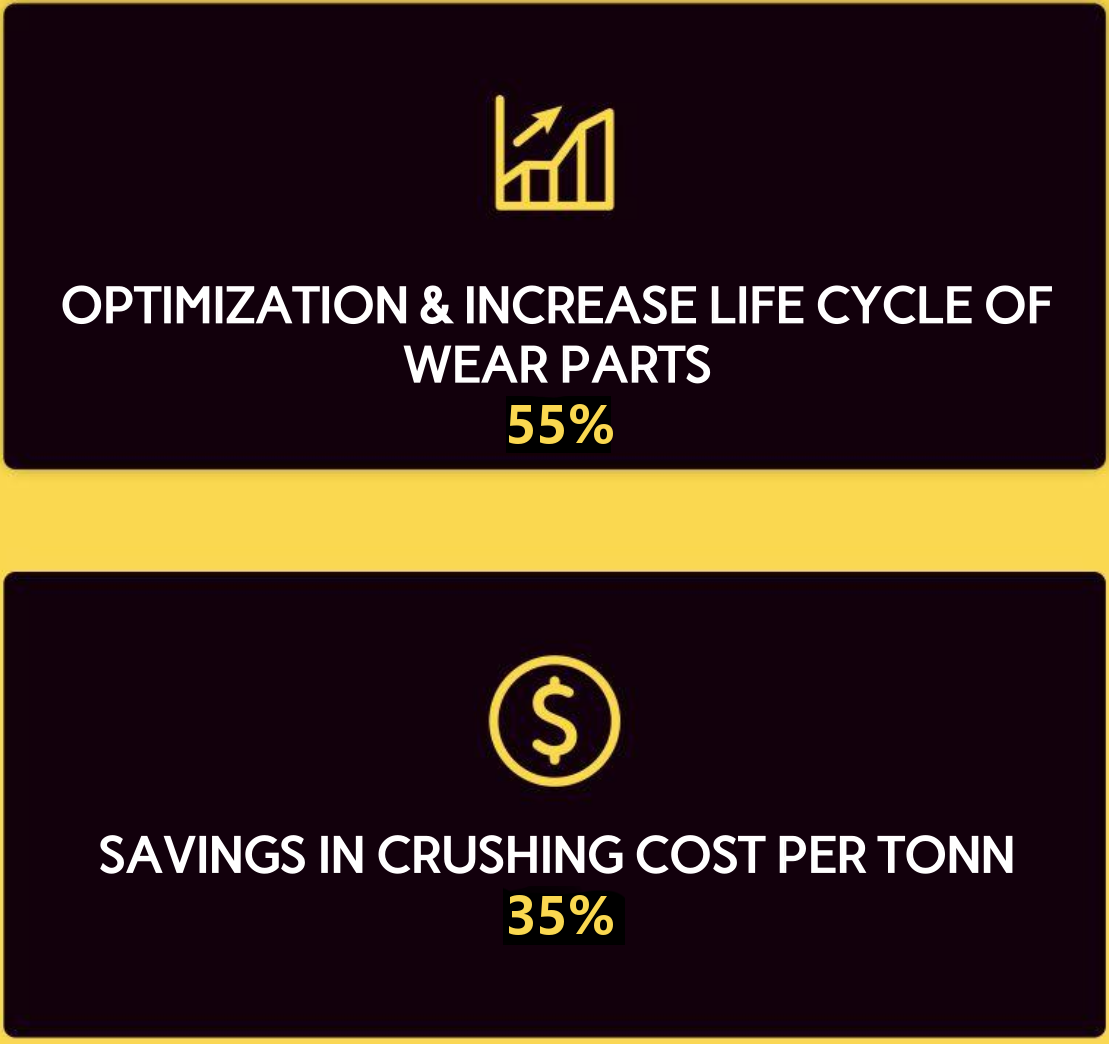
The amount of production in quarries and mines will increase by 35% in comparison with other well known wear part producers.
Our scientists have being working and researching for the aerospace and military industries for the past 50 years in the production of wear parts for the aggregates and mining industries.
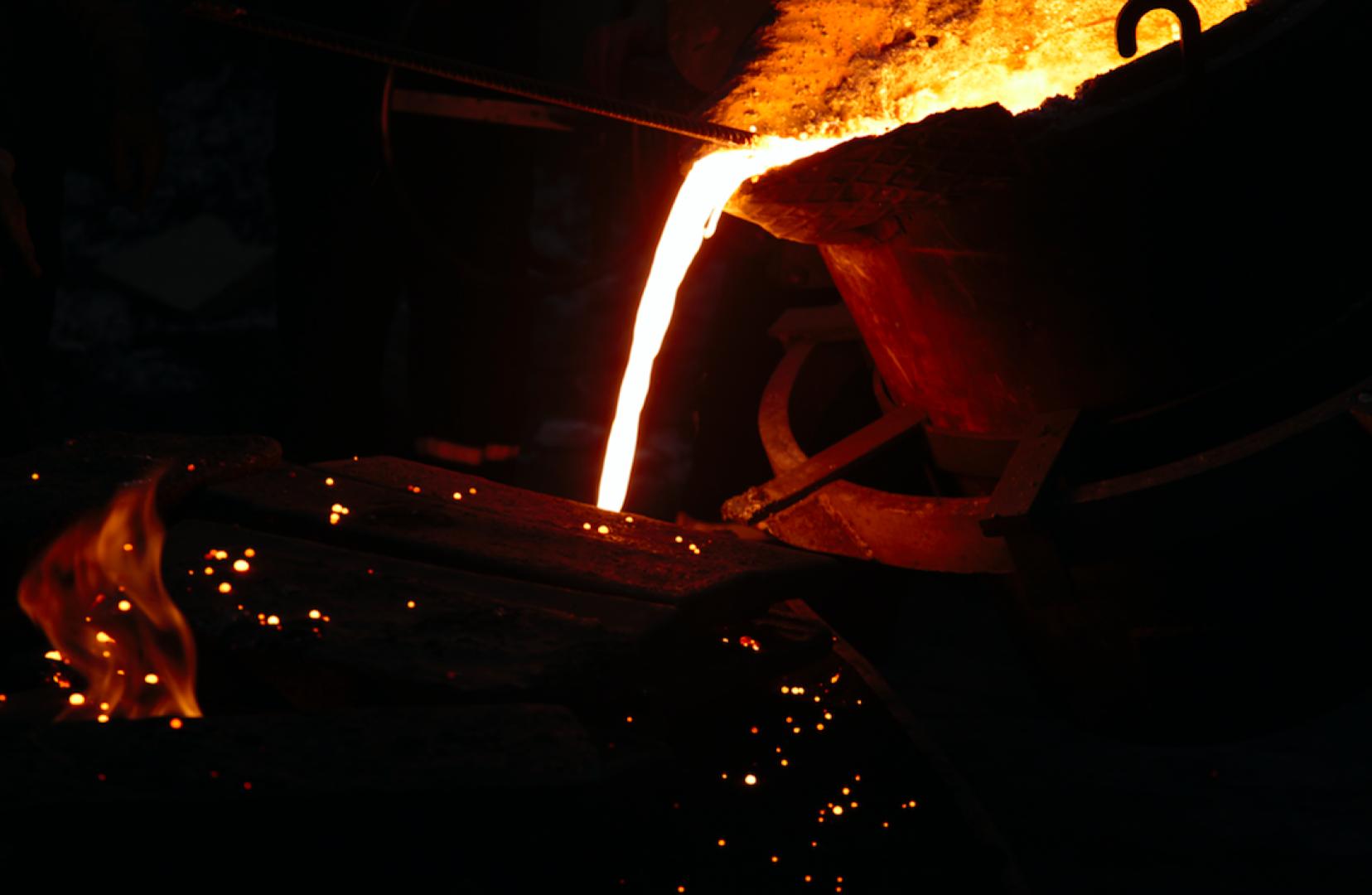
ARMET superalloys are wonder materials for metallurgical industry. By finely-tuning their composition, ARMET has been able to increase mechanical strength and improve resistance to wear and tear of the parts in any climatic environment. Armet researchers have shown that adding nanoparticles can make these materials even stronger and that’s exactly what ARMET is doing. More info: https://armet-usa.com/about-us/
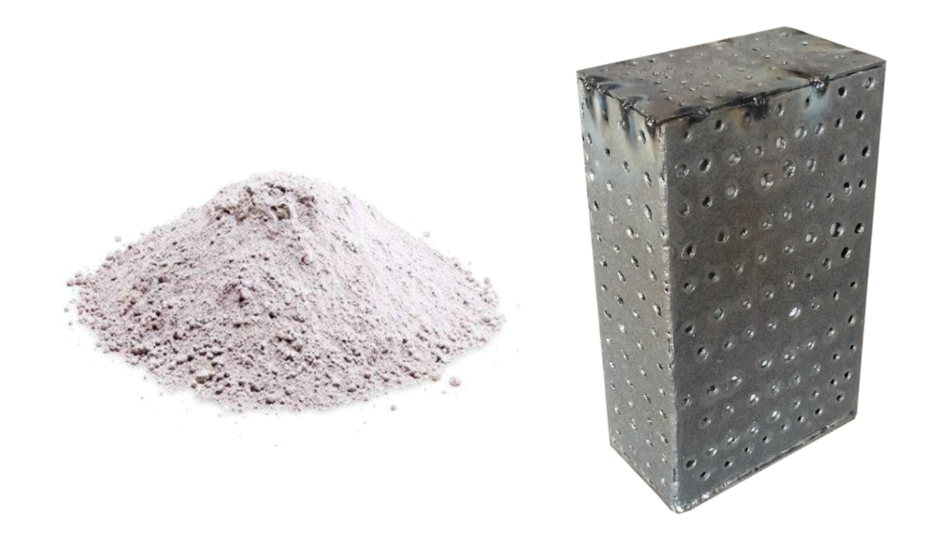
ARMET modifier is with added chromium, molybdenum, iron, niobium-tantalum, plus trace amounts of numerous other metals. ARMET modifier is used in industrial crushing applications for the aggregate and mining industries. Learn more: armet-usa.com/armet-modifers/
The improved superalloy is fabricated by a sophisticated technique with a mixture of different elements which are activated in the melting process.
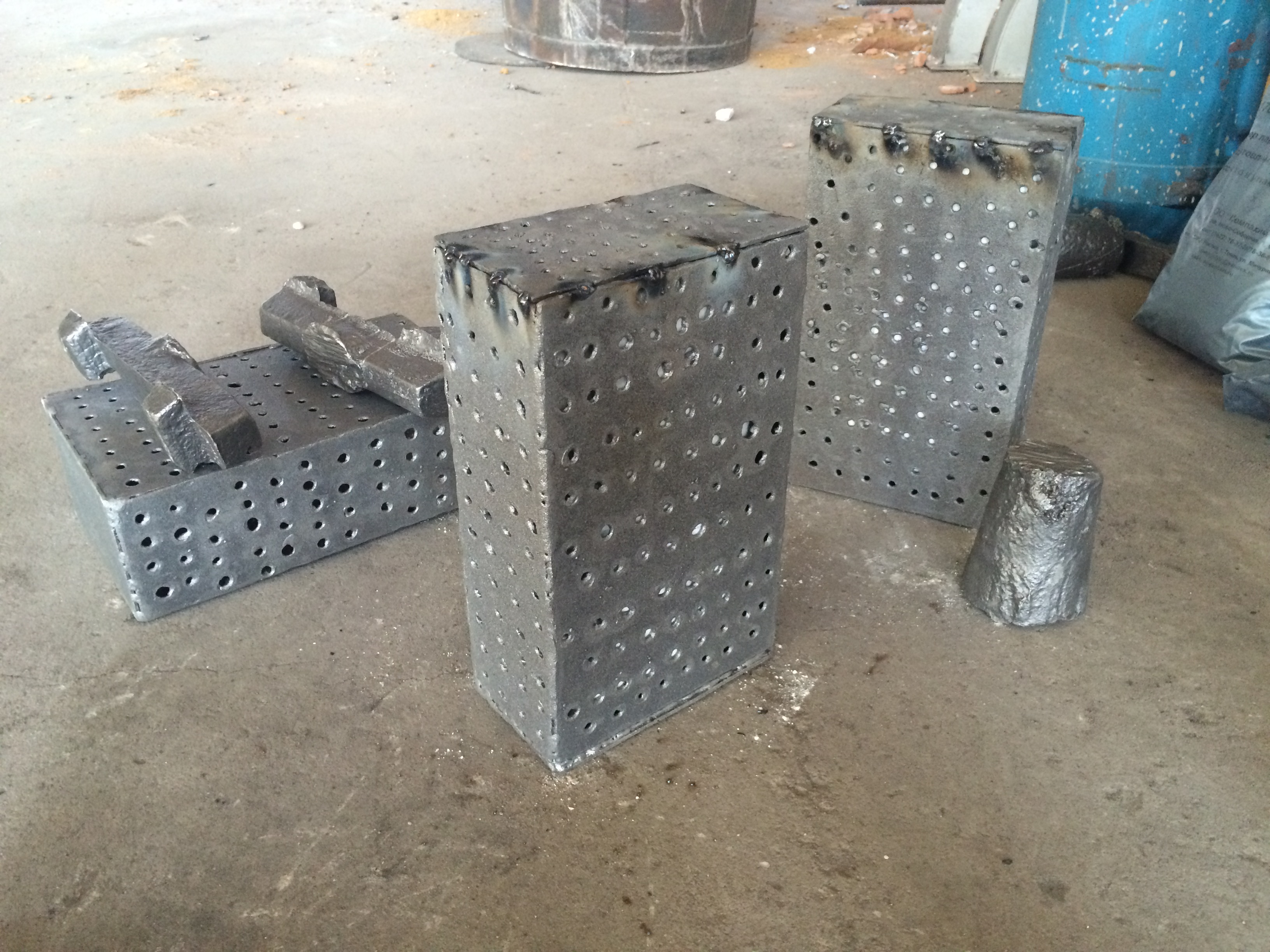
“We show that adding nanoparticles to the metal base material is an effective way to tailor the material with significantly improved physical, thermal and mechanical properties, as well as excellent performance in terms of wear and corrosion resistance,” explains ARMET Scientists.
Analysis of their sample indicated that the nanoparticles mainly aggregated at boundaries between crystalline grains of the ARMET Modifier. Mechanical testing of the sample demonstrated a significantly increased material strength, relatively high micro-hardness and good abrasive resistance.
Oswald “We will keep developing this approach and explore new composite materials reinforced with nanoparticles for additive for ARMET wear part ” .
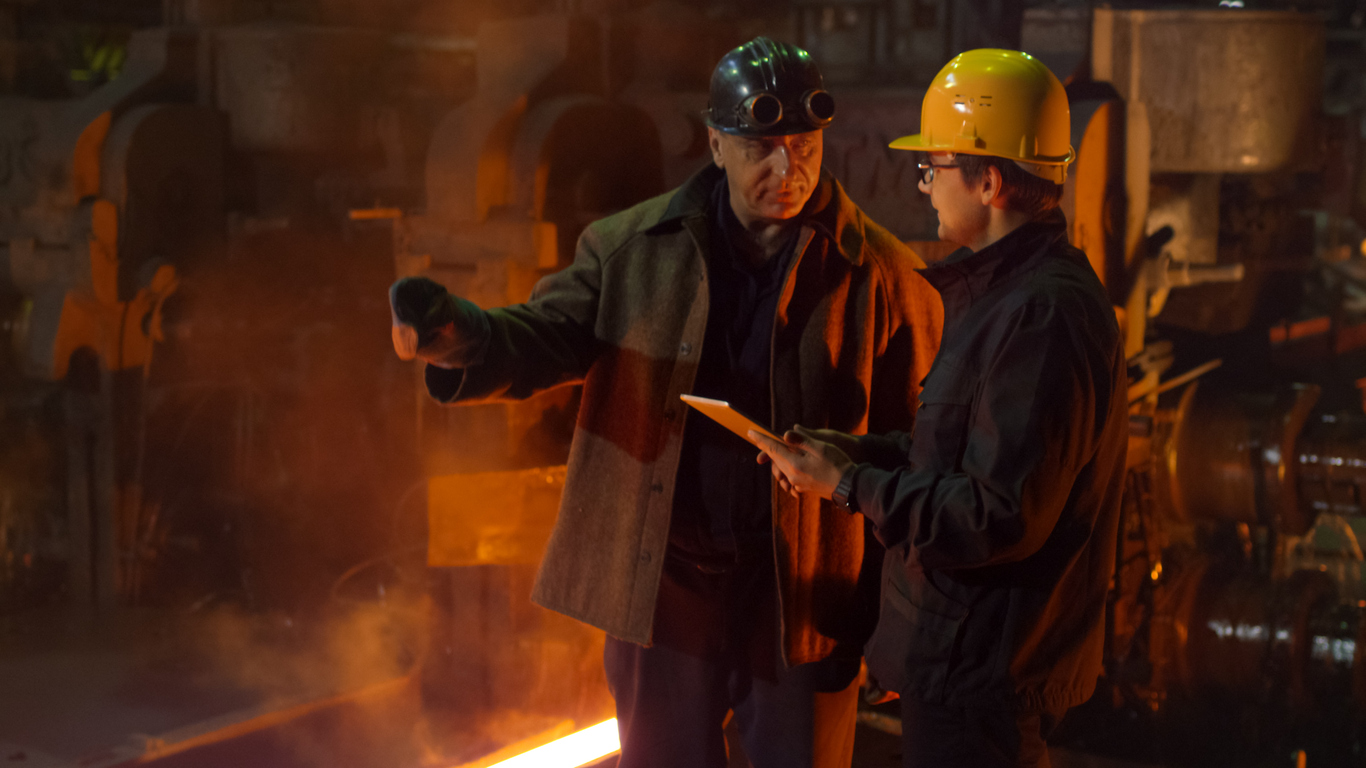
Steels with increased abrasive wear-resistance, based on high-manganese austenitic steel (Hadfield steel), obtained by additional alloying, micro alloying and modification, for producing parts highly efficient in abrasive and hydro abrasive media, that allow for substantial increases in the efficiency of parts in mining equipment, agricultural machinery, grinding and shot blasting equipment, as well as equipment which produces building materials. As an added benefit, ARMET’s wear-resistant steels do not lose their properties when operating under low temperature climatic conditions.
The new nickel-free wear-resistant ISC alloy, based on high-chromium cast iron, simultaneously features increased strength, ductility and wear-resistance. It also has good casting properties, is insensitive to overheating before tapping and during hardening, features a high casting uniformity, and has a refined dendritic structure. Applying this alloy may significantly increase the service life of products and boost the reliability of the most critical component parts, therefore the dependability of machines in general. In terms of useful life, this alloy exceeds all its counterparts manufactured using other technologies.
If you want to learn more ARMET wear parts click here: ARMET
By using ARMET wear parts you will experience
-
satisfaction with the end results
-
reduce significantly operational expenses by purchasing less wear parts for your equipment
-
produce up to 35% more than what you are currently producing
-
You will have 30% less shutdowns
Our personal approach is unique, we help our clients in every step of the way because we are here to help you succeed and grow your business by reducing your operational expenses, produce more and together build a long fruitful relationship.